Regardless of the type of a business you are running, whether it is retail, hardware, or food processing, you will need thermal ribbons. They are an essential part of your product’s packaging and can be used for long distance transportation of goods, a barcode label or as a product information label.
There are three types of thermal ribbons, wax, wax resin and resin. Their special characteristics seek different requirements when it comes to their application. Because of that, several problems might arise in the process of printing. If you are having some of the following problems, read on to find a solution for it.
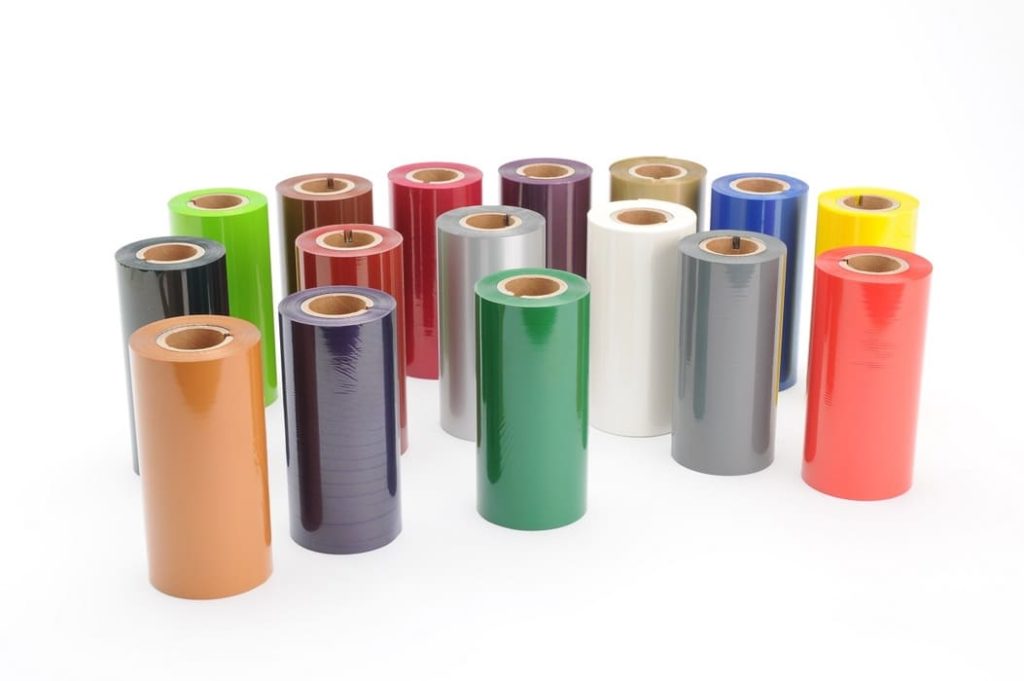
Bar Growth
The possible cause for this problem is the possibility of the print speed is set too high or the print head energy setting is too high or too low. Other possible causes are the ribbon being old or inferior or over-burnt or under-burnt. For the first symptom, it is best to reduce the printing speed or lower the print head energy setting. For the two other causes, you can try optimizing the average bar growth visually or with a verifier.
Signal (PCS) or Light Image / Insufficient Print Contrast
Possible causes for signal or light image are a faded image so the action to take is to create new label on laminated, protective stock and increase or lower the print head energy setting. Next, if a ribbon and media are incompatible you should consult a supplier for the right compatible ribbon-media combination. Another possible cause is if the printer is set on direct thermal mode in which case you should set the printer to thermal transfer mode. Finally, if there is insufficient print contrast, then you should reduce the print speed or lower the print head energy setting.
No Proper Wide/Narrow Ratio
If such situation emerges, then probably, there is not enough ribbon transfer and it causes under-burn or there is too much ribbon transfer which causes over-burn. The course of action you need to take is, for the first problem, to increase the print head energy setting or use a ribbon with a higher sensitivity whereas for the second problem, you should lower the print head energy or use a ribbon with a lower sensitivity.
“Dead Spots” on Labels
Streaks or “dead spots” on labels can happen in three cases: if the ribbon wrinkles, if the vendor misapplied stock coating or if the elements have dirt on them. In the first case, you should check the ribbon parts, increase the tension, increase the print speed and lower the print head energy setting. For the second problem, you should replace the media whereas for the third case you should clean or replace the print head.
In addition, if there are pits or voids and an inconsistent image quality because of the dirty print head, missing or worn dots on the print head or ink picking then, you should try cleaning the print head with Isopropyl Alcohol or another specialty cleaning solution or replace it altogether.
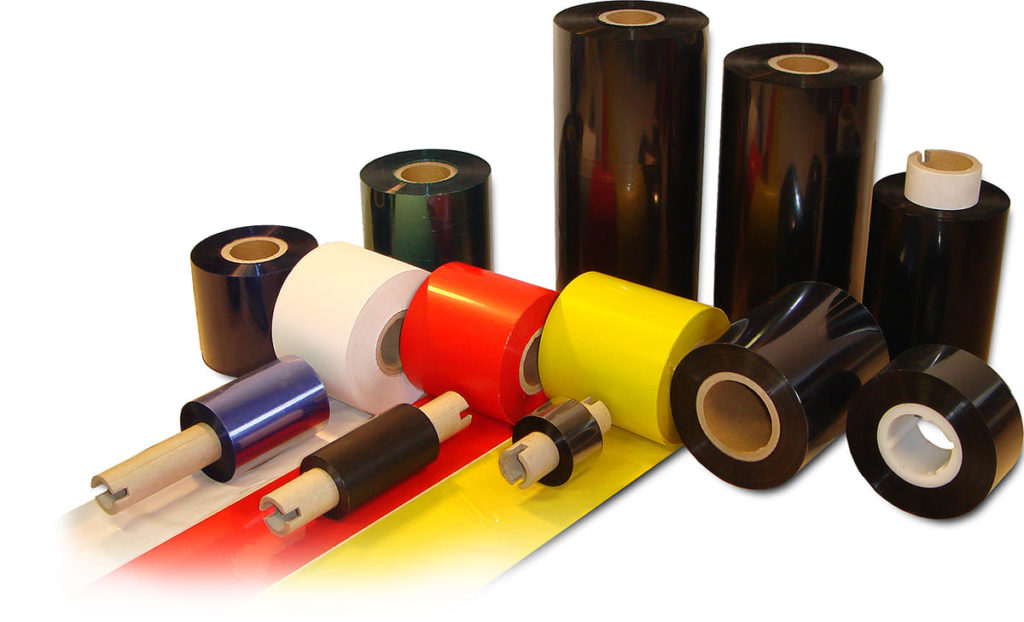
Ribbon Breaks
Ribbon breaking can happen if the print head energy is set too high in which case the energy should be reduced. Another possibility is if the print head pressure is set to high which means you need to lower it. Furthermore, the printer can be set on direct thermal mode so you need to change it on thermal transfer mode or if the unwind tension is set too high, it should be lowered. Finally, if there is not enough backcoat, you should replace the ribbon product.
Ribbon Wrinkles
There might be several possible causes if the ribbon is wrinkling. First, the print head or the guide bar might be misaligned therefore; realigning them should solve the problem. Second, there might be incorrect pressure or spring tension on the print head so you need to adjust them. Third, the print head energy setting might be set too high in which case you need to lower it. Fourth, the ribbon might be narrower than the label so you need to use a ribbon at least as wide as the label. And sixth, the rewind tension might be greater than unwind tension in which case you should adjust tension so the unwind tension is greater than rewind.